- Packaging Printing Blade Series
- Inlaid Steel Blade Series
- Tungsten Inlaid Steel Blade Series
- Pneumatic Tool Holder And Slitting Upper And Lower Tool Series
- Hot Sealing Knife Hot Cutting Knife Series
- Hard Alloy Blade Series
- Lithium Battery Blade Series
- PaperMachinery Blade Series
- Metallurgical Blade Series
- Special Shaped Blade Series
- Coating Blade Series
- Shearing Machine Bending Machine Series
The Most Comprehensive Classification of Cutting Tools
The Most Comprehensive Classification of Cutting Tools
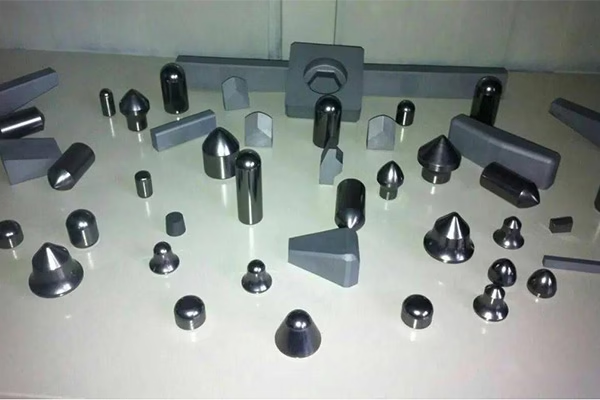
(I) Classification of Cutting Tools
Cutting tools are typically categorized by processing method and specific application into several major types, including turning tools, hole-making tools, milling cutters, broaches, threading tools, gear-cutting tools, tools for automated lines and CNC machine tools, and reamers, among others.
Cutting tools can also be classified in other ways:
By material: high-speed steel tools, carbide tools, ceramic tools, cubic boron nitride (CBN) tools, and diamond tools, etc.
By structure: solid tools, insert tools, mechanically clamped tools, and composite tools, etc.
By standardization: standard tools and non-standard tools, etc.
(II) Introduction to Common Cutting Tools
Turning Tools
Turning tools are the most widely used tools in metal cutting. They can process external cylindrical surfaces, end faces, threads, and internal holes on lathes, as well as perform grooving and parting operations. Structurally, turning tools can be divided into solid turning tools, welded assembly turning tools, and mechanically clamped insert turning tools. Mechanically clamped insert turning tools can be further categorized into machine-mounted turning tools and indexable insert turning tools. Mechanically clamped turning tools offer stable cutting performance, eliminating the need for workers to sharpen them, making them increasingly popular in modern production.Hole-Making Tools
Hole-making tools generally fall into two categories:
Tools for creating holes in solid materials, such as twist drills, center drills, and deep-hole drills.
Tools for refining existing holes, such as reamers, countersinks, and boring tools.
Milling Cutters
Milling cutters are versatile multi-edge rotary tools with many types. By application, they include:
For machining flat surfaces: cylindrical face mills, end mills, etc.
For machining grooves: vertical milling cutters, T-slot cutters, and angular milling cutters, etc.
For machining formed surfaces: convex and concave radius cutters and other complex profile milling cutters. Milling generally offers high productivity but leaves a rougher surface finish.
Broaches
Broaches are high-precision, high-efficiency multi-tooth tools widely used in mass production for machining various internal and external surfaces. Broaches can be divided into internal and external types based on the workpiece surface being machined. When using broaches, in addition to selecting the rake and relief angles based on the workpiece material and determining the broach size based on the surface dimensions (e.g., hole diameter), two parameters must be specified:
(1) Tooth rise angle (the difference in radius or height between adjacent teeth or tooth groups).
(2) Tooth pitch (the axial distance between adjacent teeth).Threading Tools
Threads can be produced by cutting or rolling methods.Gear-Cutting Tools
Gear-cutting tools are used to machine gear tooth profiles. Based on their working principle, they are divided into form gear-cutting tools (e.g., disk-type gear cutters and finger-type gear cutters) and generating gear-cutting tools (e.g., gear hobs, shaper cutters, and shaving cutters). When selecting gear hobs or shaper cutters, note the following:
(1) Basic tool parameters (module, pressure angle, addendum coefficient, etc.) must match the gear being machined.
(2) Tool accuracy should correspond to the required gear accuracy.
(3) Tool helix direction should ideally match the gear’s helix direction. For spur gears, left-hand hobs are typically used.Tools for Automated Lines and CNC Machine Tools
The cutting parts of these tools are generally similar to conventional tools, but they must meet higher requirements to adapt to CNC and automated line machining. CNC tools have evolved into three major systems: turning, drilling, and boring/milling tool systems.
(III) Common Tool Types and Applications
Turning Tools
Common turning tool tip types include:
(1) Roughing tools: For removing large amounts of material to bring the workpiece close to the required diameter. Surface finish is not critical, so the tip is ground sharp but with slight rounding to prevent chipping.
(2) Finishing tools: Produce smooth surface finishes, typically with larger nose radii than roughing tools.
(3) Round-nose tools: Versatile for various operations, including brass machining and creating fillets. Can also serve as finishing tools.
(4) Parting tools: For cutting off materials or machining grooves.
(5) Threading tools: For machining screws or nuts, available in 60° or 55° V-thread, 29° trapezoidal, and square thread types.
(6) Boring tools: For finishing drilled or cast holes to achieve precise dimensions or straightness.
(7) Facing tools: For machining workpiece end faces, with right-hand tools for shaft ends and left-hand tools for shoulder faces.Hole-Making Tools
Common drills include twist drills, flat drills, center drills, deep-hole drills, and trepanning drills. Reamers and countersinks are also considered part of this category.Milling Cutters
Types and uses:
(1) Flat-end mills: For roughing and finishing flat surfaces or contours.
(2) Ball-nose mills: For semi-finishing and finishing curved surfaces.
(3) Chamfering end mills: For roughing and small chamfers.
(4) Form cutters: Including chamfer cutters, T-slot cutters, gear cutters, and radius cutters.
(5) T-slot cutters: For machining T-slots.
(6) Gear cutters: For machining gear teeth.
(7) Roughing cutters: Designed for rapid machining of aluminum and copper alloys.Broaches
Internal broaches machine various hole profiles, such as round, square, keyway, and spline broaches. External broaches machine flat, formed, and grooved surfaces. Broaches can be solid or modular, with materials ranging from high-speed steel to carbide.Threading Tools
Threading tools include cutting tools (taps, dies, thread mills) and rolling tools (thread rollers and dies).Gear-Cutting Tools
For machining cylindrical gears, worm gears, and bevel gears, including hobs, shaper cutters, and shaving cutters.CNC Machine Tools
CNC tool systems include turning, drilling, and boring/milling tools, widely used in CNC machines, machining centers (MC), and flexible manufacturing systems (FMS).
Facebook
Twitter
LinkedIn
Table of Contents
Related Post
History and Future Trends of Cutting Tools
Cutting tools stand as both witness and catalyst in the development of human industrial civilization....
Classification and Compatibility Matching of Tool Materials and Workpiece Materials
In the field of industrial manufacturing and machining, cutting tools are defined as instruments that...
Our Company
Caleseiko stands as a global leader in mechanical blade manufacturing, renowned for its unwavering commitment to quality, innovation, and customer satisfaction. With decades of expertise, the company delivers cutting-edge blades that excel in precision, durability, and performance across diverse industries. From advanced materials to state-of-the-art production techniques, Caleseiko consistently sets new benchmarks in the industry. Their dedication to excellence and tailored solutions makes them the trusted partner for businesses worldwide.
Caleseiko: The Gold Standard in Blade Manufacturing
Innovating the Future of Cutting Technology
Precision Engineered for Unmatched Performance
Trusted by Industries Worldwide for Decades
Where Quality Meets Cutting-Edge Innovation
Caleseiko: Your Partner in Precision and Reliability